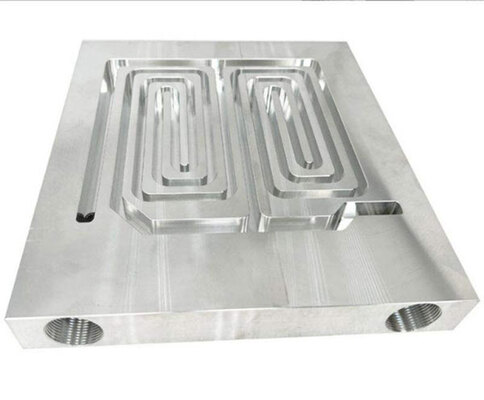
In today’s technology-driven world, managing heat in high-performance systems has become a crucial aspect of ensuring optimal functionality, reliability, and safety. From high-powered industrial machinery to electric vehicles, managing heat is no longer a luxury but a necessity. Without proper cooling, systems are prone to overheating, reduced efficiency, and potential failure. A breakthrough in cooling technology, vacuum brazed cold plates have gained considerable attention for their exceptional heat dissipation properties, making them a cornerstone in various industries requiring efficient thermal management.
At Tone Cooling Technology Co., Ltd., we specialize in providing innovative cooling solutions, with vacuum brazed cold plates at the forefront of our product line. These cold plates offer highly efficient thermal management, enabling systems to operate at their peak performance for longer periods while preventing overheating. In this article, we will delve into how vacuum brazed cold plates work, their advantages, their applications across multiple industries, and why they are revolutionizing the way we approach thermal management in high-performance systems.
What Is a Vacuum Brazed Cold Plate?
Before understanding the benefits and applications, it's essential to know what a vacuum brazed cold plate is and how it differs from conventional cooling solutions. In simple terms, a vacuum brazed cold plate is a heat dissipation component used to remove heat from electronic and mechanical systems. What makes it special is the vacuum brazing process that is used to create these cold plates.
Vacuum brazing is a high-temperature process that joins materials (usually copper, aluminum, or other metals) under vacuum conditions. This method ensures that the materials are tightly bonded without the risk of oxidation, resulting in a solid and leak-proof joint. The cold plate is designed with channels or cavities where coolant is passed through, ensuring that heat is efficiently absorbed from the device or system that requires cooling.
How Do Vacuum Brazed Cold Plates Work?
Understanding the basic working principle of vacuum brazed cold plates is essential to fully appreciate their value. Here's a step-by-step look at how these cold plates perform their cooling function:
Heat Absorption: Electronic devices or mechanical systems generate heat during their operation. A vacuum brazed cold plate absorbs this heat through its highly conductive surface, typically made of copper or aluminum. The design of the cold plate ensures a large surface area for maximum heat absorption.
Heat Transfer: Once the heat is absorbed by the cold plate, it travels through the internal channels or fins built into the plate. These channels are designed to facilitate the efficient transfer of heat to the coolant that circulates through them.
Coolant Circulation: The coolant, usually water or a specialized fluid, circulates through the channels in the vacuum brazed cold plate, picking up the heat from the device or system. This circulation process is crucial for transferring the thermal energy away from the source.
Heat Dissipation: After the coolant absorbs the heat, it is transported to a heat exchanger or another cooling mechanism where it is cooled down and ready to absorb more heat. This continuous cycle ensures that the system remains within its optimal temperature range, preventing overheating.
The vacuum brazing process plays a critical role in ensuring that the cold plate can effectively manage heat. The strong bond created through this process ensures that the cold plate remains durable and leak-proof under high pressures and temperatures.
Advantages of Vacuum Brazed Cold Plates
The use of vacuum brazed cold plates in thermal management systems offers several compelling benefits over traditional cooling methods. Let’s take a closer look at why these cold plates are becoming the preferred solution for many industries.
1. Superior Thermal Conductivity
One of the primary advantages of vacuum brazed cold plates is their exceptional thermal conductivity. The brazing process ensures a uniform and highly efficient bond between the materials used in the cold plate. This results in superior heat transfer capabilities, allowing the cold plate to absorb and dissipate heat much more effectively than other cooling solutions. This is especially important in high-power applications, such as electric vehicles and industrial machinery, where effective thermal management is essential for performance and safety.
2. Durability and Longevity
The vacuum brazing process creates strong, reliable bonds that result in highly durable cold plates. Unlike traditional soldering or welding, which can weaken over time due to temperature fluctuations or mechanical stress, vacuum brazed cold plates are resistant to corrosion, oxidation, and wear. This durability means that the cold plates can last for years without significant degradation, offering long-term, cost-effective cooling solutions.
3. Compact and Customizable Design
Another advantage of vacuum brazed cold plates is their ability to be manufactured in a variety of sizes and shapes to suit specific needs. This compact design allows the cold plates to be integrated into systems with limited space, which is often a concern in industries like aerospace and electric vehicles. Furthermore, the ability to customize the cold plates to fit unique requirements makes them a versatile solution for a wide range of applications.
4. Leak-Proof and Reliable
The vacuum brazing process ensures that the cold plates are completely leak-proof, an essential feature when dealing with high-pressure systems. The tightly bonded materials eliminate any chance of coolant leakage, ensuring that the cooling system remains effective and reliable over time. This is particularly important in challenging applications where failure can lead to significant downtime or damage.
5. Efficient in High-Temperature Environments
In environments where high temperatures are a concern, such as electric vehicles or power electronics, vacuum brazed cold plates provide a high level of thermal management. The cold plates can handle extreme heat levels, ensuring that systems maintain optimal operating conditions even in harsh conditions. This capability is especially valuable for industries that require continuous operation, such as data centers, manufacturing, and automotive sectors.
Applications of Vacuum Brazed Cold Plates
Given their high performance and versatility, vacuum brazed cold plates are used in a wide range of industries that require efficient heat management. Below are some of the key sectors that benefit from this advanced cooling technology:
1. Electric Vehicles (EVs)
In the electric vehicle industry, battery packs and power electronics generate significant amounts of heat, which can affect the performance and longevity of the components. Vacuum brazed cold plates are used to keep these systems cool, preventing overheating and ensuring that the vehicle operates efficiently. Their ability to efficiently manage the heat produced by the battery and power systems makes them an indispensable part of the EV ecosystem.
2. Data Centers and High-Performance Computing
Data centers are home to large quantities of servers and computing equipment that generate substantial heat. Cooling these systems is crucial to prevent downtime and ensure high performance. Vacuum brazed cold plates are ideal for these environments, as they can be integrated into server racks and high-performance computing systems to provide efficient, reliable cooling.
3. Aerospace and Military Applications
Aerospace and military equipment must operate under extreme conditions, including high temperatures, pressure, and vibration. Vacuum brazed cold plates are used in these sectors to maintain the temperature of critical components such as avionics, radar systems, and communication equipment. Their ability to withstand harsh conditions and provide consistent cooling is essential for mission success.
4. Industrial Equipment and Manufacturing
In heavy industrial environments, machinery and equipment often experience significant heat buildup during operation. Vacuum brazed cold plates are used in these applications to ensure that the machines run smoothly without overheating. By managing the temperature of components such as motors, sensors, and hydraulic systems, these cold plates help to prolong the life of the equipment and improve overall efficiency.
Conclusion
Vacuum brazed cold plates are revolutionizing the world of cooling technology by providing efficient, reliable, and durable thermal management solutions across various industries. Their exceptional thermal conductivity, leak-proof design, and ability to withstand high temperatures make them an ideal choice for applications ranging from electric vehicles to data centers and aerospace systems. At Tone Cooling Technology Co., Ltd., we are proud to offer cutting-edge cooling solutions that are tailored to meet the diverse needs of our clients. As technology continues to advance, vacuum brazed cold plates will undoubtedly play an even more significant role in shaping the future of high-performance systems.
Leave Your Comment & Rating Below
0 Comment(s)